Chemische Produkte sind aus unserem Alltag nicht mehr wegzudenken: Gebrauchsgegenstände aus Kunststoff, Medikamente, Waschmittel oder auch Spezialchemikalien, die in High-Tech-Produkten verarbeitet sind, machen unser Leben einfacher, komfortabler, lebenswerter. Sowohl die Grundchemikalien als auch aufwendig zu synthetisierende chemische Produkte müssen für die Massenproduktion in großtechnischen Anlagen hergestellt werden. Wir berichten, wie eine Chemieanlage aussieht und wie sie funktioniert.
Scaling-up: Wie kann eine chemische Reaktion aus dem Labor in den industriellen Maßstab übertragen werden?
Im Labor wird ein neues Produkt zunächst in kleinen Mengen synthetisiert. Hier sind es einige Milligramm oder Gramm Substanz, die umgesetzt werden, während die Industrie im Tonnenmaßstab rechnet. Die Übertragung von klein auf groß ist eine Herausforderung, die Fachkenntnisse aus dem Bereich der technischen Chemie, der Verfahrenstechnik, der chemischen Reaktionstechnik und dem Reaktorbau benötigt.
Nur im Zusammenspiel mit Fachleuten aus allen diesen Bereichen gelingt das reibungslose Scale-up.
Gleichzeitig sind die Anforderungen an Anlagen hoch in Bezug auf Betriebssicherheit, Wirtschaftlichkeit sowie Umweltschutz und nachhaltige, ressourceneffiziente Produktion – vor allem wenn es die chemische Industrie betrifft.
Die industrielle Revolution als Triebkraft für die Entwicklung der Chemietechnik
Chemische Produkte wurden vor Beginn der industriellen Revolution vornehmlich im Manufakturbetrieb hergestellt. Dazu zählten vor allem Gerbereien und Färbereien. Mitte des achtzehnten Jahrhunderts entwickelte der Engländer John Roebuck (1718-1794) mit dem Bleikammerverfahren zur Herstellung von Schwefelsäure einen der ersten industriellen Prozesse der Chemietechnik. Nur kurze Zeit später entstanden auch die ersten chemischen Fabriken, wie die „Chemische Fabrik Marktredwitz“ in Deutschland oder das „Laboratorium“ im schweizerischen Winterthur. Mit dem Aufstieg der Chemie-Industrie Anfang des 19. Jahrhunderts entwickelten sich parallel dazu die technische Chemie und der Anlagenbau. Die ersten großtechnisch hergestellten Produkte waren Schwefelsäure, Soda sowie synthetisch hergestellte Farben.
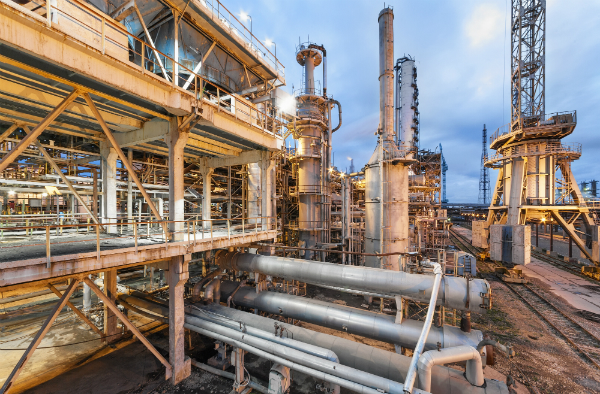
Daran erinnert auch heute noch der Name der BASF: Badische Anilin und Sodafabrik. In diese Zeit fallen viele bahnbrechende Entdeckungen im Bereich der organischen und anorganischen Chemie, wie die Synthese von Acetylsalicylsäure, eines der ersten synthetisch hergestellten Arzneimittel. Zur Produktion benötigte die chemische Industrie auch technisch immer aufwendigere Anlagen.
Ein Meilenstein der Chemietechnik ist die Entwicklung des Haber-Bosch-Verfahrens zur Ammoniaksynthese. Hierfür mussten Reaktoren entwickelt werden, die hohen Drücken und Temperaturen standhielten.
Die Übertragung in den Industriemaßstab braucht das Zusammenspiel vieler Experten
Die im Labor entwickelte Synthese ist ein erster Schritt, aber was hier funktioniert, lässt sich nicht ohne weiteres auf die großtechnische Produktion übertragen. Wichtige technische Fragestellungen für das Scale-up sind:
- die Wahl des geeigneten Reaktortyps
- die Festlegung der optimalen Reaktionsbedingungen, einschließlich der Wahl des geeigneten Katalysators
- die Entwicklung und Optimierung geeigneter Trennverfahren
Mit den technischen Aspekten befassen sich Fachleute der chemischen Reaktionstechnik, die für die Auslegung und den optimalen Betrieb chemischer Reaktoren verantwortlich sind sowie Verfahrenstechniker. Daneben steht die Wirtschaftlichkeit des gesamten Prozesses im Vordergrund, schließlich sind Verfahrensentwicklung, Bau und Betrieb einer Chemieanlage zeit- und kostenintensiv. Im Rahmen von Planung und Betrieb sind zudem sicherheitstechnische und ökologische Aspekte zu beachten sowie die juristischen Rahmenbedingungen, wozu die Einhaltung behördlicher Auflagen und gesetzlicher Vorschriften gehört.
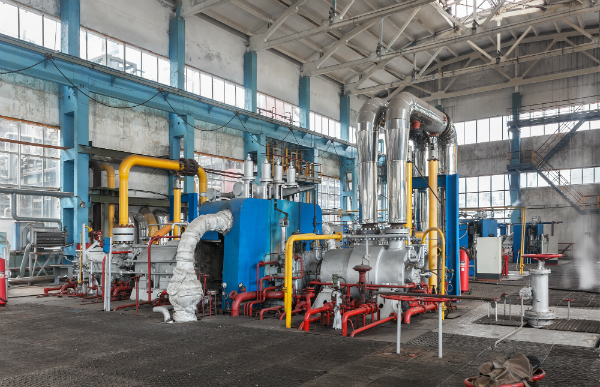
Die Funktionsweise einer typischen Chemieanlage
Die Umsetzung einer Reaktion in einer Chemieanlage verläuft normalerweise in drei Phasen.
Die Vorbereitungsphase
Diese Phase dient dazu, die Edukte (Ausgangsstoffe) optimal für die eigentliche Reaktion zu präparieren. Dazu werden die Ausgangsstoffe beispielsweise zerkleinert, zermahlen oder auch erhitzt. Die Vorbereitungen richten sich ganz nach den Anforderungen der zweiten Phase, der Reaktionsphase.
Die Reaktionsphase
Diese verläuft in speziell darauf ausgelegten Reaktoren entweder im Batch- oder im Durchflussverfahren. Für die Wahl des geeigneten Verfahrens und der optimalen Reaktorauslegung müssen verschiedene Reaktionsparameter bekannt sein, aus denen die Stoff- und Wärmebilanz errechnet wird.
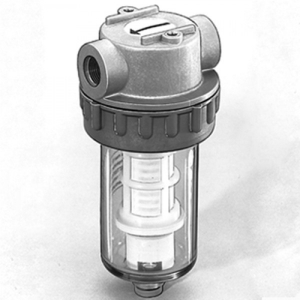
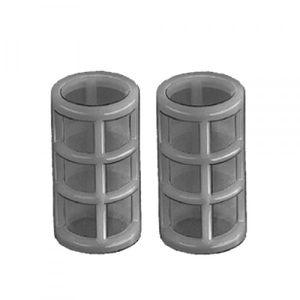
Die Stoffbilanz gibt dabei die zeitliche Änderung der Stoffmenge im Reaktor an. Dafür müssen Stöchiometrie und Kinetik unter den gewählten Reaktionsbedingungen bekannt sein. Darüber hinaus kann der maximal erreichbare Umsatz für einen entsprechend dimensionierten Reaktortyp berechnet werden und damit die tägliche Produktionsmenge eines chemischen Produktes. Die Wärmebilanz wiederum gibt die zeitliche Änderung der Wärme im betrachteten Reaktorvolumen an. Dieser Parameter ist wichtig für die Zu- oder Abfuhr von Energie während der Reaktion.
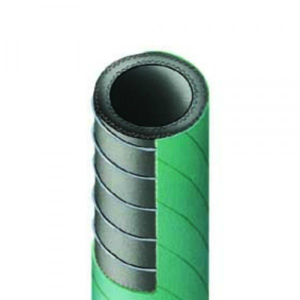
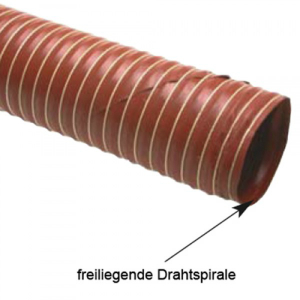
Über Druck, Temperatur und Konzentration wird die Reaktionsführung beeinflusst, aber am wichtigsten sind heutzutage jedoch Katalysatoren. Diese werden in fast allen chemischen Prozessen eingesetzt, um diese schneller und ressourceneffizienter ablaufen zu lassen.
Die Aufarbeitungsphase
Im letzten Schritt werden die gebildeten Produkte von noch vorhandenen Edukten sowie von Nebenprodukten abgetrennt. Edukte werden normalerweise wieder in die Reaktionskammer rückgeführt. Obwohl sie als das Herz einer Chemieanlage angesehen werden kann – schließlich läuft hier die eigentliche Reaktion ab – entstehen die größten Betriebs- und Investitionskosten in der Aufarbeitungsphase. Diese können bis zu 80 % des gesamten Produktionsprozesses ausmachen.
Das häufigste Trennverfahren ist die Rektifikation (Destillation), die als thermisches Trennverfahren extrem energieaufwendig und damit kostenintensiv ist.
Weitere Aufarbeitungs- und Trennverfahren sind in der Chemietechnik ebenfalls im Einsatz, so zum Beispiel die Filtration und Zentrifugation.
Die Infrastruktur einer Chemieanlage
Die hier beschriebenen drei Stufen beziehen sich auf eine einzige Chemieanlage. Damit die vor- und nachgelagerten Schritte ablaufen können, ist eine komplexe Infrastruktur um die eigentliche Produktionsanlage notwendig. In der Vor- und Nachbereitungsphase sind unterschiedliche Apparaturen notwendig, beispielsweise Laborbedarf zum Rühren und Mischen, Trocknen, Extrahieren oder Kondensieren. Der chemische Apparatebau, ein Spezialgebiet innerhalb der Chemietechnik, entwickelt die Einheiten zum Durchführen dieser sogenannten Grundoperationen.
Die einzelnen Stoffe müssen zu- und abgeführt werden, wofür spezielle Pumpen und Leitungssysteme notwendig sind. Flüssige Chemikalien und Lösungsmittel müssen in darauf ausgerichteten Tanklagern sicher untergebracht sein. Abfallprodukte und Abwässer aus einer Chemieanlage müssen gesondert entsorgt werden, wofür auf dem Werksgelände meist eigene Klärwerke vorhanden sind. Auch die Abluft einer chemischen Produktionsanlage muss über spezielle Filtersysteme gereinigt werden.
Sicherheit hat Priorität
Gerade für die chemische Industrie gelten besonders hohe Sicherheitsstandards und die gesamte Produktionsanlage muss zu jedem Zeitpunkt überwacht sein. Temperaturfühler in Reaktoren und Durchflussmesser in Rohren und Chemieschläuchen messen Zu- und Abflüsse in Echtzeit.
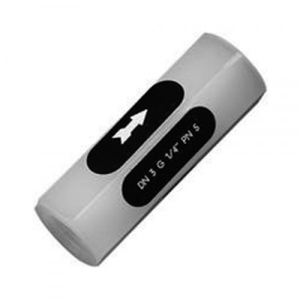
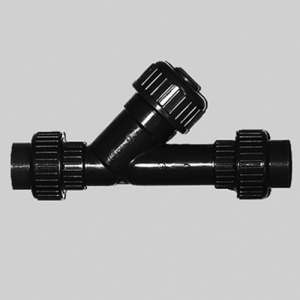
Sicherheitsventile sorgen dafür, Schlimmeres im Ernstfall zu verhindern. Alle verwendeten Materialien müssen den Anforderungen an die eingesetzte Chemie, die Temperatur oder den Druck standhalten. Dazu zählen Dichtungen für Reaktoren und Rohrleitungssysteme oder Chemieschläuche zum Weitertransport aggressiver Medien.
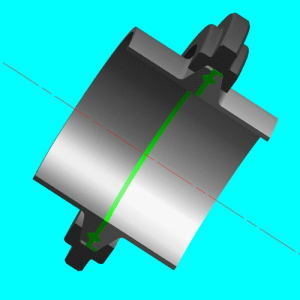
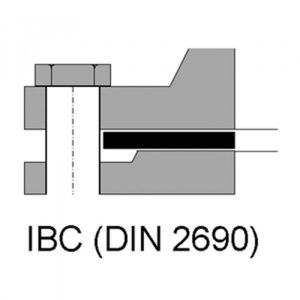
Eine Chemieanlage ist also ein hochkomplexes System, in dem alle Komponenten sicher und verlässlich arbeiten und aufeinander abgestimmt sein müssen.
Trends der Zukunft
Verschiedene Entwicklungen innerhalb der Chemie- wie auch der Verfahrenstechnik werden in Zukunft noch wichtiger werden. Dazu gehört die weitere Steigerung der Wirtschaftlichkeit der Produktion, denn der Kostendruck in diesem Bereich nimmt weiter zu. Parallel dazu sollen Energie- und Rohstoffeffizienz, wie auch in anderen Bereichen der Industrie, weiter erhöht werden.
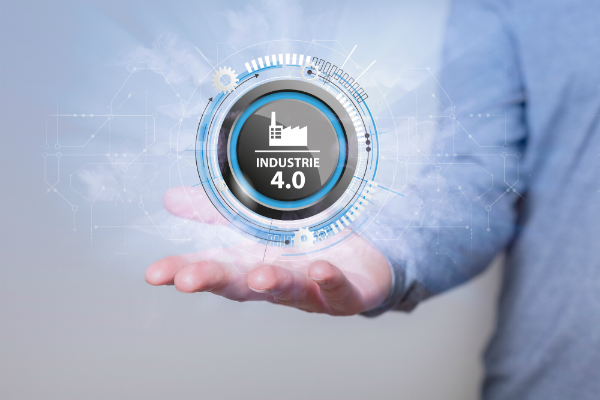
Die Miniaturisierung von Anlagen, vor allem im Bereich der Spezialchemie, gepaart mit einer zunehmenden Automatisierung und dem Einzug von „Industrie 4.0“, werden ebenfalls zu Veränderungen in Planung und Bau von Chemieanlagen führen. Schließlich werden vermehrt nachhaltige Rohstoffe in Prozessen eingesetzt und biotechnologische Verfahren gewinnen an Bedeutung. Dies bedeutet ebenfalls neue Herausforderungen für die Entwicklung verfahrenstechnischer Prozesse.