Die Kenntnis der Härte eines Materials ist für den sachgerechten Einsatz unabdingbar. Dieser Notwendigkeit folgend wurden vor allem im Laufe des letzten Jahrhunderts Härteprüfverfahren entwickelt. Eine für alle Materialien gültige Maßeinheit gibt es allerdings nicht. Die ermittelten Härtewerte hängen vom jeweils eingesetzten Prüfverfahren ab und sind nur bedingt miteinander vergleichbar.
Diamanten von anderen Planeten: Was ist das härteste Material der Welt?
Das härteste Material unserer Welt ist der Diamant, ein Fakt, der gemeinhin geläufig ist. Diamant ist eine Form des Kohlenstoffs, ein zwar häufiges chemisches Element, aber in seiner kristallinen Modifikation, dem Diamant, ein seltenes Mineral. Es entsteht unter extrem hohen Temperaturen und hohem Druck.
Wahrscheinlich gibt es aber ein noch härteres Mineral als der herkömmliche Diamant, das Mineral Lonsdaleit. Es wurde erst 1961 in dem vor etwa 50.000 Jahren durch den Einschlag eines Eisenmeteoriten entstandenen Barringer-Krater im US-Staat Arizona entdeckt. Von dieser, nach der britischen Kristallographin Kathleen Lonsdale (1903 – 1971) benannten Diamantmodifikation, konnten bisher nur Spuren gesichert werden, die für umfassende, kristallographische Untersuchungen nicht ausreichend sind. Berechnungen zufolge kann die Härte von Lonsdaleit um bis zu 58 % höher ausfallen als die von gewöhnlichem Diamant.
Auch das sehr seltene Mineral Wurtzit-Boronid, eine Modifikation des Bornitrids, die in vulkanischen Gesteinen nachgewiesen werden konnte, kann rechnerisch bis zu 18 % härter als Diamant sein. Für die Werkstoff-Forschung sind die Klärung der Bildungsbedingungen und der Strukturen von Lonsdaleit und Wurtzit-Boronid für die Entwicklung von neuartigen Werkstoffen von erheblichem Interesse.
Für die Werkstoffkunde und technische Industrie sind die Ergebnisse der verschiedenen Härteprüfverfahren wichtige Werkstoffkenngrößen. Sie erlauben den Vergleich der „Härte“ bzw. „Weichheit“ von Stählen, Polymeren und anderen Legierungen, und sind in den technischen Datenblättern der meisten Rohmaterialien zu finden. Wird beispielsweise ein sehr hartes Kunststoff-Halbzeug benötigt, etwa ein Rundstab oder eine Platte, so ist aus den technischen Datenblätter sofort ersichtlich, dass die Kunststoffe PEEK (Polyether-Etherketon) oder PVDF (Polyvinylidenfluorid) diese Anforderung erfüllen.
Die Mohs’sche Härte: Die Härteskala für Mineralien
Das älteste und bekannteste Verfahren zur Bestimmung der Materialhärte stammt aus dem Bereich der Mineralogie. Bereits im Jahr 1812 stellte der deutsche Mineraloge Carl Friedrich Christian Mohs (1773 – 1839) die erste Härteskala für Mineralien vor.
Die Mohs’sche Härteskala basiert auf einem einfachen Prinzip: Härtere Stoffe ritzen weichere Stoffe. Entsprechend dieser Beobachtung stellte Mohs eine zehnstufige, dimensionslose Skala für das Ritzvermögen bekannter, heimischer Mineralien auf, deren Härte mit denen anderer Mineralien verglichen werden können.
Mohs’sche Ritzhärte | Referenzmaterial | Bemerkungen |
1 | Talk | mit Fingernagel schabbar |
2 | Gips | mit Fingernagel ritzbar |
3 | Kalkspat | mit Fingernagel ritzbar |
4 | Flussspat | mit Messer leicht ritzbar |
5 | Apatit | mit Messer leicht ritzbar |
6 | Feldspat | mit Stahlfeile ritzbar |
7 | Quarz | ritzt Fensterglas |
8 | Topas | |
9 | Korund | |
10 | Diamant |
Dem Diamant als härtestes Mineral ordnete er die Härte 10 zu, dem Talk als weichstes Mineral, ein Magnesiumsilikat, die Härte 1. Die Mohs’sche Härteskala wird auch heute noch in der Mineralogie angewendet. Für Materialuntersuchungen kommen jedoch andere, dem Material angepasste und sehr viel präzisere Härteprüfverfahren zum Einsatz.
Moderne Härteprüfverfahren: Statische vs. Dynamische Härteprüfung
Generell ist bei der Bestimmung der Materialhärte zwischen dynamischen und statischen Prüfverfahren zu unterscheiden.
Bei dynamischen Prüfverfahren nutzt man die schlagartige Belastung der Probe durch eine dynamische Krafteinwirkung. Die Härte wird anhand der Eindringtiefe eines Prüfkörpers, den Intender, in das zu untersuchende Material ermittelt oder aus seiner Rücksprunghöhe, wenn er unter definierten Bedingungen auf die Probe fällt.
Bei der statischen Härteprüfung kommt es hingegen zu einer stoßfreien, gleichbleibenden Belastung des Werkstoffs durch den Prüfkörper. Die Härte ergibt sich entweder aus der Eindringtiefe des Prüfkörpers oder der Vermessung seines Abdrucks im Material.
Die Prüfverfahren sind nicht für alle Werkstoffe gleichermaßen geeignet, so dass Härteangaben nur für das jeweilige Prüfverfahren gültige Werte darstellen.
Rockwell-Härte: Die Methode für harte Materialien und Metalle
Die Rockwell-Härteprüfung ist ein statisches Härteprüfverfahren, das bevorzugt bei sehr harten Werkstoffen Verwendung findet, sich jedoch auch für weniger harte Materialien eignet. Es wurde von den beiden US-amerikanischen Metallurgen Stanley P. Rockwell (1886 – 1940) und Hugh M. Rockwell (1890 – 1957) entwickelt.
Als Prüfkörper werden spitzwinklige Diamantkegel oder Hartmetallkugeln genutzt. Für die Härtebestimmung wird der Prüfkörper zunächst mit einer Druckkraft, der „Prüfvorkraft“ (F0), belastet, wobei er in den Werkstoff eindringt. Nachfolgend wird die Druckkraft bis zum Erreichen einer vorgegebenen „Hauptkraft“ (F1) erhöht, wodurch der Prüfkörper tiefer in den Werkstoff eindringt. Die Differenz zwischen beiden Eindringtiefen ist die bestimmende Maßgröße für die Rockwell-Härte (HR, engl.: Hardness Rockwell).
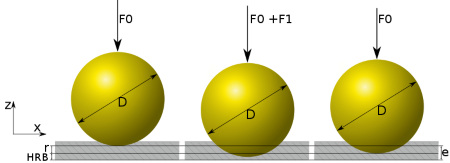
In alphabetisch geordneten „Rockwell-Skalen“ A bis D sind die von den Prüfbedingungen, den Druckkräften und der Art des Prüfkörpers abhängigen Rockwell-Härtewerte HR tabelliert. So erreichen beispielsweise die Klingen japanischer Kochmesser aus wolframhaltigem Aogami-Stahl nach der Rockwell-Skala C die Material-Härte HRC 67. Klingen gewöhnlicher Haushaltsmesser haben dagegen nur eine durchschnittliche Material-Härte von HRC 55.
Brinell-Härteprüfung: Die Alternative für Materialien mit unebener Oberfläche
Die Brinell-Härteprüfung ist ebenfalls ein statisches Verfahren, das von dem schwedischen Ingenieur Johan August Brinell (1849 – 1925) zur fünften Pariser Weltausstellung im Jahre 1900 der Fachwelt vorgestellt wurde. Diese Methode, mit der ein weiter Härtebereich erfasst werden kann, wird bevorzugt bei Materialien mit grober oder unebener Oberfläche eingesetzt, da sie im Gegensatz zur Rockwell-Härteprüfung weniger anfällig für Oberflächenunebenheiten ist. Die Brinell-Härteprüfung ist daher auch die Standard-Methode der Forstwirtschaft zur Bestimmung der Härte von Hölzern.
Bei der Brinell-Härteprüfung wird der Prüfkörper, eine Hartmetall-Kugel, senkrecht auf die Probe gedrückt. Dabei hinterlässt sie einen Abdruck, dessen Fläche mikroskopisch vermessen wird. Die Brinell-Härte (HB) errechnet sich aus der Prüfkraft und der Abdruckfläche des Prüfkörpers. Heimische Hölzer erreichen Brinell-Härten bis zu HB 4, für Tropenhölzer werden Werte bis zu HB 6 gemessen. Für Chrom-Nickelstähle ergeben sich dagegen Brinell-Härten um HB 200.
Vickers-Härteprüfung: Optische Methode mit Diamantprisma
Die Vickers-Härteprüfung geht auf den englischen Gießerei-Unternehmer Edward Vickers (1804 – 1897) zurück. Im Gegensatz zur Brinell-Härtebestimmung kann die Vickers-Härte (HV) auch für die Untersuchung sehr harter Materialien wie Keramik und Hartmetall eingesetzt werden.
Bei der Vickers-Härteprüfung wird wie bei der Brinell-Härteprüfung die Abdruckfäche des Prüfkörpers auf dem zu untersuchenden Material als Maß für die Härte vermessen. Der wesentliche Unterschied zur Brinell-Härteprüfung ist die Verwendung eines pyramidalen Diamantprismas als Eindringkörper, der für den gesamten Härtebereich geeignet ist, statt kugelförmige Eindringkörper aus Hartmetall, deren Größe sich nach dem jeweils zu untersuchenden Material richtet.
Die Vickers-Härte für Normal-Stähle liegt im Bereich von HV 350 bis HV 380, für Feingold, das als besonders weich gilt, sind Vickers-Härten unter HV 70 gängige Werte.
Shore-Härte: Die Härtemessung von Kunststoffen
Das statische Shore-Härte Prüfverfahren wurde 1915 von dem US-amerikanischen Ingenieur Albert Ferdinand Shore (1876 – 1936) für die Untersuchung von Kunststoffen entwickelt. Es basiert auf der Messung der Eindringtiefe eines genormten Stahlstiftes als Prüfkörper in das Material bei festgelegter Prüflast und -zeit.
Für die Untersuchung weicher Kunststoffe läuft der Stift zu einem Konus aus, für harte Kunststoffe, wie PE (Polyethylen), zu einer Spitze. Die gemessenen Werte werden als Shore-Härte (HS) bezeichnet und je nach eingesetztem Prüfkörper mit dem Buchstaben A für weiche Kunststoffe oder D für harte Kunststoffe gekennzeichnet.
Typische Werte für weiche, gummielastische Kunststoffe wie Synthese-Kautschuke liegen zwischen Shore A 50 bis 70°. Solche Polymere werden u.a. zur Fertigung von Gummimatten und Dichtungen herangezogen. Für harte Kunststoffe, wie PE (Polyethylen), PP (Polypropylen) und PC (Polycarbonat), sind Werte bis Shore D 80° charakteristisch. Aus diesen werden u.a. harte Kunststoffschläuche, Schlauchverbinder und andere Formteile gefertigt.
Leeb-Härte: ein nahezu universelles Prüfverfahren
1978 stellte der deutsche Materialwissenschaftler Dietmar Leeb ein dynamisches Härteprüfverfahren vor, das sich besonders für den mobilen Einsatz eignet und nach ihm benannt ist: die Härteprüfung nach Leeb. Das dynamische Verfahren basiert auf der elektronischen Messung der Differenz zwischen der Abschuss-Geschwindigkeit eines normierten Prüfkörpers auf das zu untersuchende Material und der verminderten Rücksprung-Geschwindigkeit des Prüfkörpers infolge der elastischen Verformung des Materials beim Aufprall. Der Parameter-Variabilität von Abschuss-Geschwindigkeit und Größe des Prüfkörpers ist es zu verdanken, dass das Verfahren nahezu universell einsetzbar ist. Die jeweils ermittelte Leeb-Härte (HL) ist in die dafür gängigen Härtewert-Skalen nach Rockwell (HR), Brinell (HB), Vickers (HV) und auch Shore (HS) näherungsweise wandelbar.
Hitze und andere Faktoren können die Materialhärte beeinflussen
Die Härte eines Materials ist keineswegs eine feste Größe. Auch Umwelteinflüsse wie Temperatur und Luftfeuchtigkeit und auch die Einwirkung von radioaktiver Strahlung können Einfluss auf die Materialhärte nehmen. Ein simples Beispiel ist das Erweichen der Asphaltdecke der Straßen und Autobahnen unter langanhaltender Hitzeeinwirkung im Sommer. Durch erhöhte Umgebungstemperaturen verringert sich die unter herkömmlichen Temperaturen ausreichende Materialhärte der Fahrbahn mit der Folge von Fahrbahnschäden und damit erhöhtem Unfallrisiko für den Autofahrer.
Aus diesem Grund werden alle Härteprüfungen nach strikten Standards durchgeführt, die inzwischen als EU-Normen verbindlich sind. Die normgerechte Bestimmung der Materialhärte erfolgt heutzutage mit zertifizierten Prüfgeräten, die nicht nur im Material-Prüflabor, sondern auch unter Industriebedingungen verlässliche Werte liefern. Nur so sind die Härtewerte auch sichere Parameter für den vorgesehenen Einsatz eines Materials.
Bild-Quellen: Beitragsbild | © Surasak – stock.adobe.com Rockwell-Härteprüfverfahren | © Djhé, CC BY-SA 3.0 <https://creativecommons.org/licenses/by-sa/3.0>, via Wikimedia Commons