Wer Sport macht oder im Regen unterwegs ist, schätzt Funktionskleidung, die Wasser abhält und atmungsaktiv ist. Brillengläser, die leicht zu reinigen sind oder Töpfe, die nichts anbrennen lassen, sind uns ebenso im Alltag willkommen. Doch nicht nur im privaten Bereich wird Polytetrafluorethylen (PTFE) geschätzt, auch die Industrie setzt diesen Hochleistungskunststoff vielfältig ein. Unter allen Fluorkunststoffen ist PTFE der mit Abstand am häufigsten hergestellte mit einem Anteil von 52 % und einer Produktionsmenge von 140.000 t im Jahr (Stand: 2015).
Die Entdeckung geschah zufällig…
Bis heute hält sich die Mär, dass PTFE für die Raumfahrt entwickelt wurde. Zwar waren die Hitzeschutzkacheln der Apollo-Kapseln tatsächlich mit einer Schutzschicht aus diesen Polymeren ausgerüstet, aber entdeckt wurde dieser Kunststoff viel früher. 1938 suchte der Forschungs-Chemiker Dr. Roy J. Plunkett (1910 – 1994), der bei dem US-amerikanischen Chemiekonzern El du Pont de Nemours & Company beschäftigt war, nach einem neuen Kühlmittel für Kühlschränke und experimentierte dafür auch mit Tetrafluorethen. Er bewahrte das farblose und ungiftige Gas, gekühlt mit Trockeneis und unter hohem Druck, in flaschenförmigen Zylindern auf. In einem dieser Zylinder kam es zur Polymerisation.
Als Plunkett das gleichsam über Nacht entstandene weiße Produkt näher untersuchte, stellte er fest, dass es von keiner Chemikalie angegriffen wurde, weder von heißen Säuren und Laugen, noch von jeglichen Lösungsmitteln. Im Jahr 1941 wurde Polytetrafluorethylen zum Patent angemeldet, das seitdem von DuPont unter dem Markennamen Teflon® produziert und exklusiv vertrieben wird.
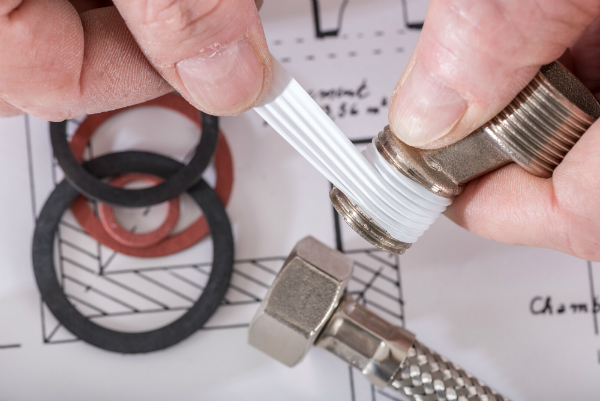
1943 wurde für das „Manhattan-Projekt“, dem geheimen Militärprojekt zur Entwicklung und dem Bau der amerikanischen Atombombe, ein Korrosionsschutz für die Behälter gesucht, in denen Uranhexafluorid gelagert werden sollte. Einzig das von Plunkett gefundene Polymer erwies sich als dafür geeignet.
Nach dem 2. Weltkrieg wurde der Einsatzbereich auf zivile Anwendungen ausgeweitet und so fand es auch seinen Weg in die Küche. Der Ingenieur Marc Grégoire und seine Frau Colette kamen auf die Idee, Bratpfannen und Kochtöpfe damit zu beschichten. Die Idee setzte sich durch und beide gründeten unter dem Markennamen Tefal® ein Unternehmen, das fortan diese Beschichtungstechnologie nutzte. Der Siegeszug des PTFE als ein nahezu unverwüstlicher Kunststoff begann. Sein Erfinder, der amerikanische Chemiker Roy J. Plunkett, wurde hoch geehrt und 1985 in die „Hall of Fame“ der bedeutendsten Erfinder aufgenommen.
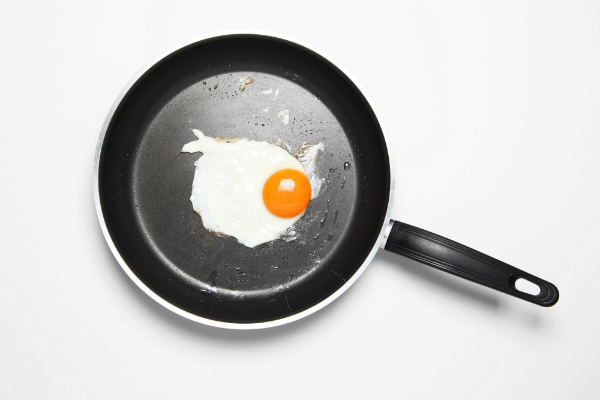
Herstellung und Weiterverarbeitung
Ausgangsstoff für alle fluorierten Polymere ist Flussspat (CaF2). Dieses wird in einem ersten Schritt mit Schwefelsäure zu Flusssäure (HF) und Calciumsulfat (CaSO4) umgesetzt. In einem zweiten Schritt folgt die Reaktion der Flusssäure mit Chloroform (CHCl3) zu Tetrafluorethylen (F2C=CF2), das sich in einer radikalischen Polymerisationsreaktion in wässriger Lösung zu Polytetrafluorethylen umsetzt.
Polytetrafluorethylen gehört zwar zu den Thermoplasten, kann aber nicht durch thermische Verfahren weiterverarbeitet werden, denn bevor es schmilzt, fängt es bei Temperaturen oberhalb von 400°C an sich zu zersetzen.
Deshalb werden PTFE-Granulate in Formen verpresst und unter kontrollierten Bedingungen zu Halbzeugen, wie Platten, Folien und Bänder gesintert. Die Halbzeuge können anschließend mit spanabhebenden Verfahren, wie Bohren, Fräsen, Drehen oder Schälen, weiterbearbeitet werden.
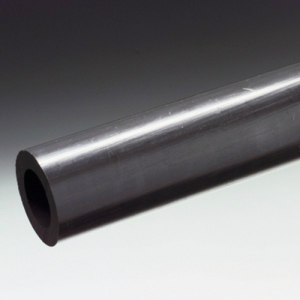
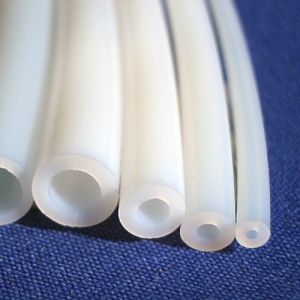
PTFE-Schläuche, Mikroschläuche, Spaghetti-Schläuche und Rohre werden durch Ramextrusion hergestellt, einem speziellen Kolbenstrang-Pressverfahren für Thermoplaste mit sehr hoher Schmelzviskosität, das auch für die Verarbeitung von PTFE-Granulat geeignet ist.
Hochleistungskunststoff mit einzigartigen Eigenschaften
Nicht angreifbar und sehr beständig
Polytetrafluorethylen nimmt unter den Kunststoffen eine Sonderstellung ein. Nur elementares Fluor und geschmolzene Alkalimetalle greifen diesen Kunststoff an. Gegenüber allen anderen Chemikalien ist er inert. Witterungseinflüsse, UV-Strahlung oder Ozon führen bei vielen Kunststoffen zu Alterung und Versprödung, nicht aber bei Polytetrafluorethylen.
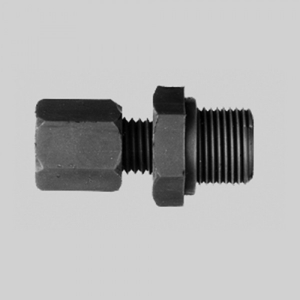
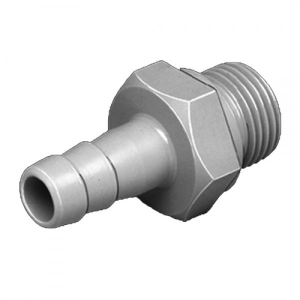
Bauteile aus diesem Kunststoff sind korrosionsbeständig und über den weiten Temperaturbereich von -200 °C bis zu +250 °C im Dauerbetrieb einsetzbar. Vor allem im chemischen Anlagenbau werden diese Eigenschaften geschätzt und Polymerbeschichtungen aus PTFE für Behälter oder Rohre genutzt. Auch Schläuche, Dichtungen oder Armaturen aus diesem Polymer werden vielfältig eingesetzt.
Physiologisch unbedenklich und aalglatt
Bereits seit 1960 hat Polytetrafluorethylen die FDA-Zulassung für den Lebensmittelbereich und wird für Schläuche oder als Innenbeschichtung für Rohre und Behälter eingesetzt. Gleiches gilt für die Pharmaindustrie und die Biotechnologie. In der Medizintechnik werden nicht nur Schläuche, sondern auch Stents und Gehäuse von Herzschrittmachern aus Polytetrafluorethylen eingesetzt. Denn dieses Material ist nicht nur physiologisch unbedenklich, sondern auch antiadhäsiv.
Aufgrund der extrem niedrigen Oberflächenspannung bleiben weder Flüssigkeiten noch Feststoffe daran haften.
Der Reibungskoeffizient von PTFE ist äußerst niedrig – das Material ist im wahrsten Sinne des Wortes „aalglatt“. Diese Eigenschaft ist sehr nützlich, wenn reibungsarmes Gleiten notwendig ist. Die Industrie verwendet daher Beschichtungen aus dem Kunststoff für Gleitlager oder Transportbänder.

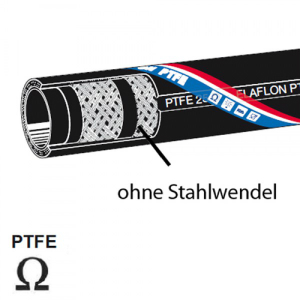
Aufgrund des niedrigen Reibungskoeffizienten kommt es außerdem zu einem „Selbstschmiereffekt“, was bedeutet, dass keinerlei Schmiermittel erforderlich sind, was zusätzlich Kosten erspart. Auch das Rückgleiten, der sogenannte „Slip-Stick“-Effekt, der auftritt, wenn sich die Oberflächen zweier Körper gegeneinander bewegen, ist stark abgemindert. Schließlich wird das Polymer auch für die Ummantelung von Drähten oder Kabeln in der Elektrotechnik eingesetzt, da es nicht nur thermisch stabil sondern auch elektrisch isolierend ist.
Maßgeschneiderte Anwendungen
Aber einen bedeutenden Nachteil hat PTFE gegenüber vielen anderen Kunststoffen: Bereits unter geringer Druckbelastung ist der Kunststoff nicht mehr formstabil. Der Kaltfluss, so nennt man die irreversible Deformation von Materialien unter Pressdruck, sowie das „Kriechen“ unter Druckbelastung sind zwei unerwünschte Eigenschaften des Kunststoffs. Denn Dichtungen sollten nicht nur gegen eine Vielzahl an Chemikalien beständig sein, sondern auch unter Druck ihre Form behalten.
Durch den Zusatz von Füllstoffen können die Eigenschaften von PTFE verbessert und auch das Kaltfließen verhindert werden.
So erhöht Graphit die Druckfestigkeit und Härte, verbessert die Gleit- und Verschleißeigenschaften und verringert den Oberflächenwiderstand, was für Gleitlager, Ventilsitze im chemischen Apparatebau oder allgemein für Konstruktionsteile mit antistatischen Anforderungen wichtig ist. PTFE-Compounds können ferner auch Füllstoffe wie Keramik, Glas oder organische Füllstoffe wie Polyimid (PI), Polyetheretherketon (PEEK) oder Polyphenylsulfon (PPSO2) enthalten.
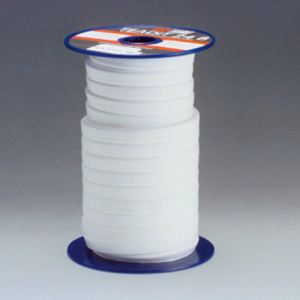
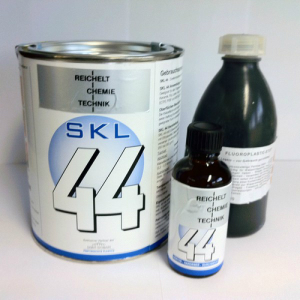
Aufgrund seiner chemischen Inertheit und Hydrophobie ist das Fügen von Werkstücken aus Polytetrafluorethylen nicht ganz einfach. Das Press-Schweißen, ein Verfahren bei dem unter hohen Druck und bei Temperaturen zwischen 370 °C und 390 °C gearbeitet wird, ist das einzige Schweißverfahren, welches für PTFE geeignet ist.
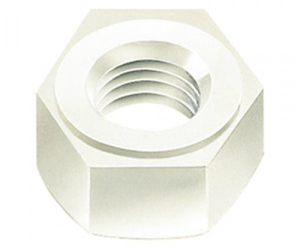
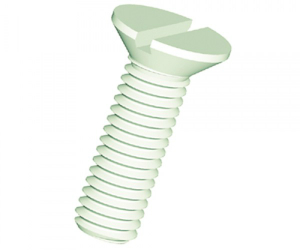
Für das Verkleben von Werkstücken ist eine spezielle Vorbehandlung der Fügeflächen mit einem sogenannten Primer notwendig, der die glatte, hydrophobe Oberfläche chemisch aufraut, sodass sich eine festhaftende, stabile Kleberbrücke zwischen den Werkstücken ausbilden kann. Für sichere Klebeverbindungen stehen heute industriell erprobte PTFE-Kleber-Kits auf der Basis von Epoxidharzen, Cyanacrylaten oder synthetischem Kautschuk zur Verfügung.
Vom Recycling zum geschlossenen Kreislauf
Kunststoffabfälle werden zum großen Teil in Verbrennungsanlagen thermisch verwertet.
Der Grund dafür ist die Vielzahl chemisch sehr unterschiedlicher Kunststoffe, die nur sortenrein wieder nutzbar gemacht werden können.
Für reine PTFE-Abfälle ist die thermische Verwertung wenig sinnvoll, denn abgesehen von dem geringen Heizwert des PTFE entstehen hierbei stark korrosive und toxische Fluorverbindungen, wie Fluorwasserstoff, Trifluoressigsäre und Fluorphosgen, die eine aufwändige, chemische Nachbehandlung der Verbrennungsgase erfordern.
Da PTFE jedoch vielfach auch als Überzüge auf Metallen eingesetzt wird, wie PTFE-beschichtete Rohre oder Bleche, ist die thermische Behandlung solchen Metallschrotts vor dem Einschmelzen unumgänglich. Diese Arbeiten erfolgen in speziell dafür ausgelegten Anlagen.
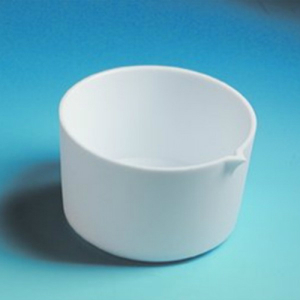
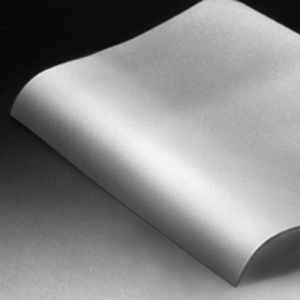
Die Rückgewinnung von PTFE aus gewöhnlichen Kunststoffgemischen ist aufgrund des hohen spezifischen Gewichts des Kunststoffs weniger problematisch und lässt sich beispielsweise durch Flotationsverfahren technisch gut realisieren. Derartiges PTFE ist aber meist so stark verunreinigt und als Compound auch noch durch Zuschlagstoffe belastet, dass seine Wiederverwertung an Grenzen stößt. Es wird deshalb meist nur noch als Zuschlagstoff im Bauwesen genutzt.
Bereits 2010 hatte der Lehrstuhl für Werkstoffverarbeitung der Universität Bayreuth ein Verfahren vorgestellt, bei dem PTFE-Abfälle in Monomere aufgespalten und in den Produktionsprozess rückgeführt werden.
Das Verfahren eignet sich nicht nur für die Aufarbeitung sortenreiner Polytetrafluorethylen-Abfälle, sondern auch für PTFE-Compounds und PTFE-haltige Mischabfälle.
Damit stellt das Verfahren den geschlossenen Kreislauf her, der nicht nur ökologisch gefordert, sondern auch ökonomisch sinnvoll ist.