Sintern ist ein Herstellungsverfahren, welches bereits sehr lange bekannt ist und verbreitet angewandt wird. Die Herstellung von Keramik, wie das Brennen von Kaolin zu oder Ton zu Töpferwaren, sind Sinterverfahren, die empirisch gefunden und seit ihrer Entdeckung immer weiter verfeinert wurden. Heutzutage wird dieses Fertigungsverfahren nicht nur für Keramiken, vor allem für technische Keramiken, sondern auch für die Fertigung von Sinterwerkstoffen aus Metallen und Kunststoffen angewandt. Durch Sintern können Halbzeuge und spezielle Form- und Bauteile hergestellt werden, wie Sinterplatten, Sinterscheiben und Sinterrohre zur Filtration von aggressiven Gasen und Flüssigkeiten. Sie kommen nicht nur im Chemielabor zum Einsatz, sondern auch in der chemischen, biotechnischen und pharmazeutischen Industrie. Darüber hinaus haben Formteile aus Sintermaterialien, vor allem aus Sintermetallen, im Maschinen- und Automobilbau Eingang gefunden.
Das Prinzip der Sinterung
Den Sinterprozess kann man sich als ein „Zusammenbacken“ von pulverförmigen oder granulierten Ausgangsstoffen bei höheren Temperaturen vorstellen. Genauer betrachtet ist dieses Fertigungsverfahren jedoch komplexer und läuft in mehreren Phasen ab.
Durch die Auswahl des eingesetzten Ausgangsmaterials, seiner Korngröße sowie der Prozessparameter kann die Porengröße sehr genau vorbestimmt werden.
1. Phase beim Sintern: Formgebung
Zunächst werden die pulverförmigen oder granulierten Ausgangsstoffe zu sogenannten „Grünlingen“ geformt oder gepresst, wobei sie bereits die Form der gewünschten Sinterprodukte erhalten. Wichtig ist, dass schon dabei eine möglichst homogene Packungsdichte erreicht wird und dass die Pulverpartikel fest aneinander haften. Sollte dies nicht der Fall sein, so muss zusätzlich ein organisches Bindemittel zugegeben werden. Um einen „Grünling“ herzustellen, stehen prinzipiell drei grundlegende Verfahren zur Verfügung: Das trockene oder feuchte Verpressen der Ausgangsstoffe unter hohem Druck, das Formgießen der in Wasser aufgeschlämmten Ausgangsstoffe, das Schlickergießen, und die sogenannte plastische Formgebung.
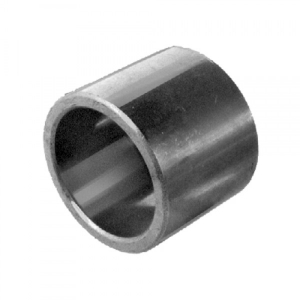
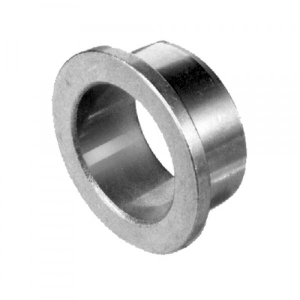
Der Vorgang beim Verpressen
Das Verpressen der Ausgangsstoffe bei Drücken von einer Tonne pro Quadratzentimeter und mehr kann durch Trockenpressen oder Feuchtpressen erfolgen. Im ersteren Fall enthält das Ausgangsmaterial wenig Feuchtigkeit, der Wassergehalt liegt hier unter 7%. Beim Feuchtpressen ist er mit über 12% höher, allerdings muss dann der „Grünling“ vor der Sinterung ausreichend getrocknet werden.
Welches Presserfahren zur Anwendung kommt, hängt unter anderem von der Geometrie der herzustellenden Halbzeuge ab.
Das Feuchtpressen ist bei komplizierteren Geometrien empfohlen, während die Trockenpressung für einfachere Bauteile meist ausreichend ist. Beim einseitigen Pressen wird das pulverförmige Ausgangsmaterial mit einen Stempel durch Druck auf ungefähr ein Drittel seines ursprünglichen Volumens verdichtet. Da die Kraft nur von einer Seite wirkt, erfahren die Ausgangsstoffe beim Pressen keine durchgängig gleichmäßige Verdichtung.
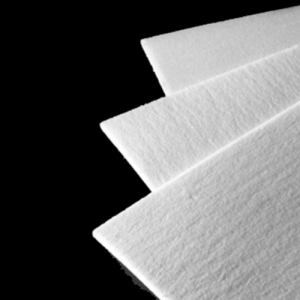
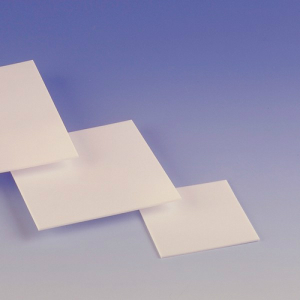
Das uniaxiale Pressen wird deshalb fast nur für die Produktion flacher, plattenförmiger Sinter-Halbzeuge aus Polyethylen (HDPE), Polytetrafluorethylen (PTFE) sowie aus Bronze und Cr-Ni-Stahl genutzt. Um eine gleichmäßigere Verdichtung zu erhalten, werden beim Pressen zwei Stempel eingesetzt, die das pulverige Ausgangsmaterial von oben und unten zusammendrücken. Dieses „zweiseitige“ Pressen wird auch als „koaxiales Pressen“ bezeichnet. Über dieses Fertigungsverfahren können beispielsweise axial vorzugsgerichtete Magneten hergestellt werden.
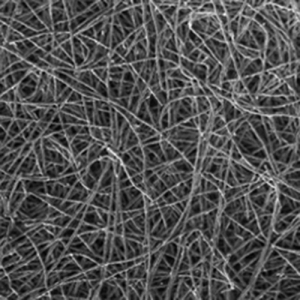
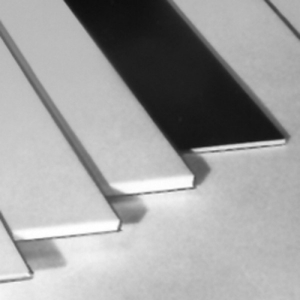
Bereits während des Pressvorgangs wird dabei das Magnetpulver magnetisch ausgerichtet. Die anisotropen Eigenschaften bleiben beim anschließenden Sintern erhalten. Wird hingegen auf den Grünling von allen Seiten gleichmäßiger Druck ausgeübt, spricht man vom „isostatischen Pressen“.
Die damit hergestellten Werkstoffe haben eine hohe, gleichmäßige Verdichtung sowie isotrope, richtungsunabhängige Eigenschaften.
So funktioniert das Gießen
Außer dem Pressen stehen verschiedene Gießverfahren zur Herstellung der Grünlinge zur Verfügung, die weitere Möglichkeiten der Formgebung ermöglichen. Diese eignen sich vor allem für kompliziertere Geometrien. Die Herstellung von Keramik, Tonzeug oder Porzellan sind Beispiele für das Gießverfahren, bei dem der sogenannte Schlicker, die in Wasser aufgeschlämmten Ausgangsstoffe, in Gipsformen abgegossen wird. Dabei nimmt die Gipsform das Wasser auf. Der so hergestellte, feste Grünling kann anschließend weiterverarbeitet werden. Auch das „kalte Gießen“, bei dem zur Ausgangsmasse ein zusätzliches Bindemittel wie z.B. ein Epoxidharz zugegeben wird, gehört zu diesen Verfahren.
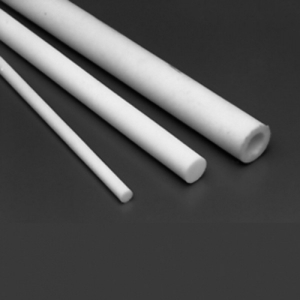
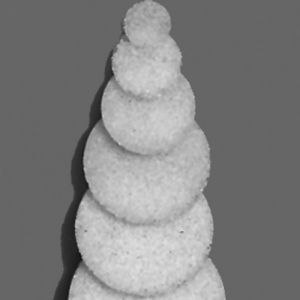
Das Keramikspritzgussverfahren ist ein Beispiel für die plastische Formgebung. Hierbei wird dem Ausgangsstoff, dem keramischen Pulver, ein thermoplastischer Kunststoff als Bindemittel zugegeben und durch Spritzgießen in die gewünschte Form gebracht. Anschließend kann der Grünling gesintert werden. Die Kunststoffbeimengung verbrennt während des Sinterns. Ähnlich funktioniert auch der Metallpulverspritzguss – nur wird hier statt Keramikpulver als Ausgangsmaterial feines Metallpulver, beispielsweise Chrom-, Nickel- oder Eisenpulver oder Pulver von Metalllegierungen, wie Messing und Edelstahl eingesetzt.
Mit dieser speziellen Technik können komplex geformte Teile präzise geformt und sehr effizient vorgefertigt werden.
2. Phase beim Sintern: Verdichtung
Nach der Formgebung der Ausgangsmaterialien durch Pressen, Gießen oder plastisches Formen erfolgt das Sintern. Die Grünlinge müssen zunächst vorgetrocknet werden, insbesondere dann, wenn sie durch Feuchtpressen hergestellt wurden. Daran anschließend erfolgt die eigentliche Sinterung. Je nachdem, welche Ausgangsmaterialien vorliegen, sind unterschiedlich hohe Sintertemperaturen erforderlich. Normalerweise liegen die Sintertemperaturen kurz unterhalb der Schmelztemperatur des Ausgangsmaterials. Für technische Keramiken reichen die Temperaturen bis zu 1600 °C, für Metalle und Metalllegierungen können diese niedriger sein. Normalerweise liegen sie kurz unterhalb der Schmelztemperatur. Der Sintervorgang verläuft unter Schutzgasatmosphäre oder im Vakuum in drei Phasen ab.
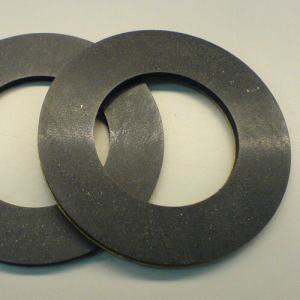
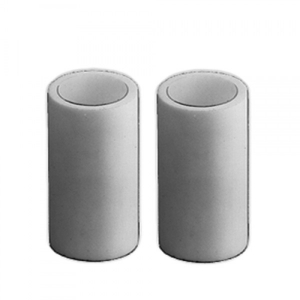
Umordnung von Teilchen
Zu Beginn der Sinterung kommt es durch Diffusion und Umordnung zur Bildung von ersten Kontaktstellen zwischen den Teilchen. Es bilden sich sogenannte „Hälse“ aus, indem sich die Partikel des Ausgangsmaterials aneinander lagern und dadurch insgesamt ihre Oberfläche verkleinern. Dieser Vorgang ist energetisch begünstigt und läuft daher freiwillig ab. Dabei nimmt die Dichte des Werkstoffs langsam zu.
Als Faustregel gilt ein Zuwachs von 10 %.
Das Material verdichtet sich
In der zweiten Phase der Sinterung setzt sich das „Halswachstum“ fort, wobei sich die Pulverkörnchen vergrößern und weiter miteinander verschmelzen. Dadurch kommt es zu einer erheblichen Verdichtung des Materials um bis zu 30 %. Gleichzeitig bilden sich beim Sintern Poren oder ganze Kanalsysteme aus über die noch im Grünling eingeschlossene Gase nach außen entweichen.
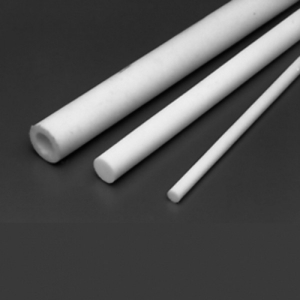
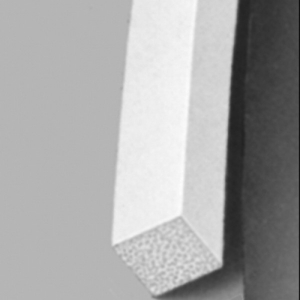
Porosität nimmt ab
In der dritten Phase erfolgt der Übergang zu einer immer mehr geschlossenen, dichteren Porosität. Gleichzeitig wachsen die Pulverkörnchen weiter. Nunmehr kann es zu einem unerwünschten „Riesenkorn-Wachstum“ kommen, was die Materialeigenschaften ungünstig beeinflusst. Auch hier nimmt die Dichte noch in geringem Maße zu. Deshalb muss der Sinterprozess rechtzeitig unterbrochen werden.
Anschließende Arbeitsschritte – was folgt der eigentlichen Sinterung?
Nach dem Sintern erfolgt die Abkühlung. Danach kann eine Nachbearbeitung erfolgen, insbesondere dann, wenn es sich um Bauteile handelt, die nur in einem bestimmten technischen Toleranzbereich einsetzbar sind. Dazu können die Teile auch nochmals unter hohen Drücken und Temperaturen in Form gepresst werden.
Weitere Nachbearbeitungen, wie sie bei anderen Fertigungsverfahren in der Formteiltechnik notwendig sind, entfallen.
Für welche Produkte wird Sinterung eingesetzt?
Sinterung ist für die rationelle, materialsparende Herstellung vieler Produkte geeignet – zum Beispiel für Bauteile aus Keramiken für die Elektroindustrie oder auch für präzise Form- und Bauteile aus Sintermetallen, wie sie in der Automobilindustrie, etwa als Bremsklötze, zum Einsatz kommen.
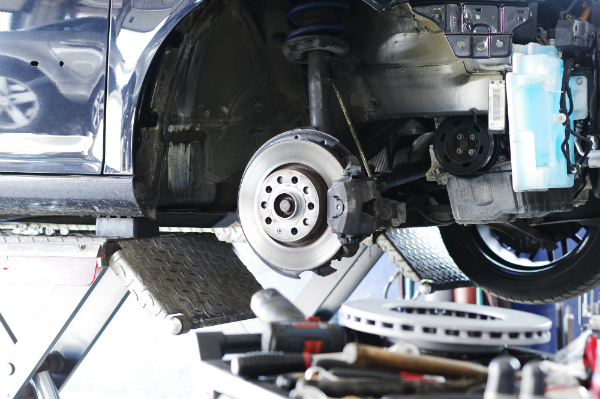
Auch für die Produktion von Magneten und zur Herstellung von Dentalkeramik wird die Sintertechnik genutzt. Schließlich werden Sinterplatten und Sinterscheiben sowie Sinterrohre aus Kunststoffen, wie HDPE, LDPE oder PTFE, im chemischen Labor und im Apparatebau zur Klarfiltration von Prozesslösungen und in der Reinraumtechnik als Luftfilter eingesetzt.
Lasersintern – ein Fertigungsverfahren speziell für Kunststoffe
Diese spezielle Form der Sinterung ist für bestimmte Kunststoffe möglich. Dazu werden die Granulate schichtweise aufgetragen und jeweils unmittelbar gesintert. Auf diese Weise ist der Aufbau von feinen dreidimensionalen Strukturen möglich.

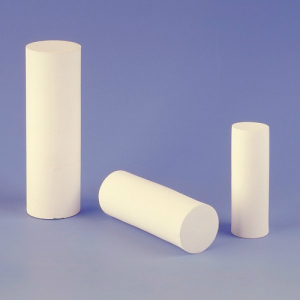
Durch die große Auswahl der Werkstoffe und Materialien ist Sintern in der Formteiltechnik universell einsetzbar. Schließlich ist das Verfahren sehr materialeffizient, da kein Ausschuss anfällt, sondern sich das gesamte eingesetzte Material im Produkt wiederfindet.